在大型兆瓦级涡轮机中,轴承座圈的轴向裂纹非常普遍,这种损坏会将轴承寿命缩短至一至两年,最近的研究发现了轴向裂纹的根本原因,使预防和早期检测成为可能。
现代风力涡轮机是我们能源组合的重要组成部分,不幸的是,变速箱寿命问题影响了风力涡轮机的稳定,轴承座圈中的轴向裂纹已成为最新一代风力涡轮机齿轮箱过早故障的主要原因,然而在其他行业中,很少发现齿轮箱轴承出现轴向裂纹故障,为什么风力涡轮机中的损坏如此普遍,一直是一个谜,也是一个深入研究的主题,在找到解决方案之前,必须了解根本原因。
本文的第一部分回顾了关于轴向裂纹的最新研究,并讨论了轴向裂纹如何从切割和蚀刻时呈白色的较小裂纹中生长出来,白色蚀刻裂纹(WEC)起源于显微超硬区域,在切片和蚀刻时也会呈现白色,这些裂纹开始的区域被称为白色蚀刻区域(WEA)损伤,最近的几篇论文表明,必须超过快速和严重塑性变形的阈值,才能创建这些硬微观WEA。
高速和中速轴承内圈的轴向裂纹已成为风力涡轮机齿轮箱寿命问题的主要原因,过去几年中,许多关于轴向裂纹的技术论文都集中于为什么这种不寻常的轴承现象在风力涡轮机齿轮箱中如此普遍。
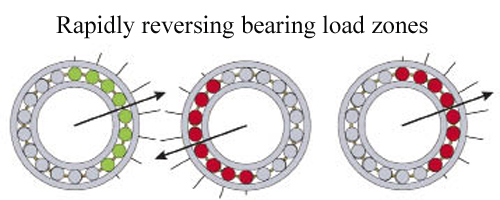
对齐的(绿色)滚柱位于装载区,未对齐的滚柱(红色)与加载的滚柱成180°,在瞬时扭矩反转中,未对齐的滚柱突然加载,然后卸载,并在短时间内重复加载。
风力涡轮机轴承的选择符合20年的设计寿命,故障可能性很低,大多数制造商遵循德国劳埃德船级社齿轮箱轴承指南,德国劳埃德船级社要求对齿轮箱轴承进行滚动接触疲劳(RCF)分析,得出的计算寿命至少为130000小时,故障可能性低于10%。

如果变速箱满足这些设计标准,那么轴向开裂故障率怎么会如此高,并且经常在运行的第一年或第二年内发生?使用充分理解和验证的方法进行了分析的轴承怎么可能比预测的更早失效?答案在于轴向开裂失效模式不同于经典RCF失效模式,RCF故障是由轴承材料损坏引起的,这种损坏随着时间的推移以众所周知的速度累积,轴向开裂失效是相对较新的现象,其失效模式的了解要少得多。
轴承的轴向开裂失效模式主要发生在通常以过盈配合安装到轴上的内圈上,环在装配到轴上时被加热,当环冷却时,它会收缩——将环固定到位,但也会在环中产生拉伸应力,从而增加轴向开裂的可能性,安装过程中过度的环向应力可能会导致内圈的轴向裂纹失效,但这在风电行业中似乎不是一般情况,当轴承被切割和蚀刻时,裂纹边缘的微观白色区域是一个关键指标,表明这不仅仅是标准环向应力失效,这些裂纹被称为WEC,通常在硬化轴承座圈中发现,当WEA损伤导致剥落或剥落时,可称为白色结构剥落(WSF),这通常发生在碳化管道中,无论哪种方式,损害都始于WEA的创建。
对轴向裂纹轴承的详细失效分析表明,WEA不仅出现在表面裂纹中,也出现在地下裂纹中,甚至出现在裂纹尚未开始的区域,WEA损伤实际上是内圈材料的微观结构变化,在滚道表面下方产生微小的超硬区域(比周围区域硬30%至50%),这些区域就像钢中的夹杂物。

圆锥滚子轴承内圈出现白色蚀刻裂纹和白色表面剥落,有证据表明,两者都是由钢地下的WEA微观结构变化引起的,一旦事件引发地下WEA形成,轴承的正常滚动作用可在这些夹杂物状区域的交界处引发裂纹,裂纹不可避免地扩展到表面并成为WEC,WEC在滚道上轴向扩展并导致轴承过早失效。
许多研究论文认识到WEA损伤的两种主要机制,即氢诱导WEA和应力诱导WEA,氢WEA被认为是由腐蚀、水污染、电流或腐蚀性油添加剂驱动的,一旦表面出现裂纹,这些添加剂会使裂纹恶化,但是,是什么事件引发了这些表面裂缝?本文侧重于理解可引发地下应力诱发WEA损伤的事件,但也将说明这些事件如何导致氢诱发WEA也可能发生的裂缝。
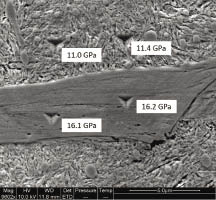
轴承内圈中应力引起的WEA损伤来自于导致滚子在快速应变率的同时施加高的表面应力的事件,最近研究中提到的可能的WEA机制包括冲击载荷,即可能导致高应力和应变的突然载荷;表面牵引力,即滚子和座圈之间的摩擦接触,产生高表面和地下应力;严重塑性变形(SPD),即地下应力高到足以引起微观变形;快速塑性变形(绝热剪切带–ASB),即地下塑性变形如此之快,以至于产生的热量无法消散,从而直接改变材料以形成铁素体微观结构。
这四种机制是相关的,可以同时发生,例如,WEA损伤可以通过弹道冲击在实验室中产生,其中所有四种WEA机制都被证明是同时作用的。
绝热剪切带(ASB)是基材内的一个区域,在快速和严重的塑性变形过程中,通过微观局部加热而转变。自20世纪60年代以来,由于ASB作为一种失效模式在高速金属成形和切割、各种类型的弹道冲击以及车辆碰撞等领域的重要性,ASB得到了广泛的研究。绝热,一个热力学术语,简单地说就是没有热传递——产生的热量保留在产生热量的区域。这些剪切带通常较窄,约为0.0002至0.020英寸。在钢中,这些带实际上是疲劳裂纹引起的WEA损伤。存在瞬时高应力和应变率的阈值,其中微观塑性变形产生的热量如此之快以至于无法逃逸。地下金属在冷却时会瞬间软化并转变为改变的微观结构。缓慢发生的严重变形会使热量逸出,不会产生ASB或WEA损伤。因此,冲压金属零件可能表现出与弹孔相似程度的塑性变形,但如果应变率足够慢,冲压零件可避免ASB和WEA损坏。
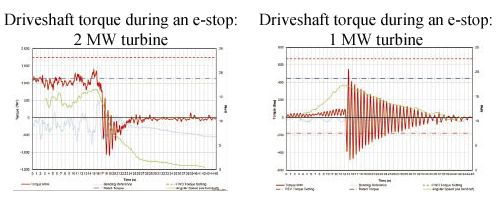
左图:红色轨迹描绘了2 MW风力涡轮机上的大风TTR事件。在大约17秒的标记处,扭矩迅速从正转变为负。该扭矩直接通过齿轮箱轴承传递。
右图:红色轨迹描绘了1 MW风力涡轮机在紧急停机期间的大风TTR事件。在大约15秒标记处,扭矩从正到负振荡。
在轴承材料中,快速塑性变形产生的热量会导致硬化轴承钢的微观结构转变为一条超硬铁素体,在切割和蚀刻时呈现白色–WEA损伤。然而,WEA损伤带不需要使轴承失效。这种WEA损伤的一小部分可以作为一种夹杂物,引发WEC,最终传播到表面并穿过轴承滚道表面。
轴承制造商通过提高产品所用钢材的纯度和质量,不断提高滚子轴承的寿命。通过尽量减少硬夹杂物和桁条(细长碳化物或硫化物夹杂物),制造商可以尽量减少裂纹产生和扩展的潜在位置。根据轴承制造商用于计算L10寿命的标准RCF方法,这些努力使轴承寿命提高了10倍。不幸的是,所有制造超洁净钢的努力都被风力涡轮机运行中引发WEA损伤的事件所浪费,模拟了低于滚道表面0.04英寸(1mm)的夹杂物。该深度与滚子正常赫兹载荷期间轴承滚道下的最大剪切应力深度一致。这也是夹杂物类杂质的最坏可能位置——导致轴承表面疲劳寿命缩短和轴向裂纹。一旦开始,WEA损伤可将轴承寿命缩短至使用标准滚动接触疲劳公式计算的预测寿命的1%至10%。这一解释说明了WEA引起的轴向裂纹如何在运行几年内导致轴承故障。
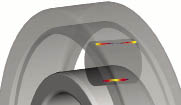
黄色和红色区域表示瞬时扭矩反转期间轴承中的最高应力位置。
风力涡轮机中的哪些事件会产生足以引发WEA损坏的冲击载荷和快速塑性变形?最近NREL的一篇论文总结道,“风力涡轮机暴露在极端事件下,例如断电或紧急停机,可能会产生ASB形成所需的局部变形能量。”
最近对轴承轴向开裂的研究表明,冲击载荷和紧急停机可能是WEA损坏的原因。长期以来,风力专业人员一直认识到突然停机与所有涡轮驱动组件的极端负载之间的联系。许多人还注意到紧急停机与齿轮箱寿命之间的关系。此外,人们越来越认识到,严重停车事件期间的瞬态扭矩反转(TTR)可能是齿轮箱轴承中损坏冲击载荷的来源。
其他类型设备中的一些驱动系统在轴承未受到WEA损坏的情况下,会出现严重的瞬时负载和扭矩反转。没有反转的严重扭矩负载以及以受控方式缓慢发生的扭矩反转不会在轴承滚道中产生快速塑性变形。然而,风力涡轮机不同。为什么?它们的驱动系统在扭矩反转的严重程度上是独一无二的,最重要的是它们发生的速度。
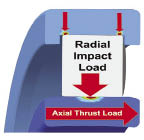
在带有螺旋齿轮的齿轮箱中,已知错位滚子的同时径向冲击和轴向载荷会降低轴承寿命。
涡轮传动系是什么原因导致它如此容易受到快速和严重的扭矩反转的影响?这与叶片和发电机转子的相对旋转质量(惯性)以及它们如何在驱动系统的扭振固有频率内相互作用有关。典型的涡轮机在叶片中具有80%至90%的相对惯性,其余大部分惯性在发电机转子中。正常运行时,叶片正向驱动发电机。电网断开、紧急停机或强风停机会触发叶片的快速空气制动,从而试图使驱动系统减速。大部分空气制动力用于减速巨大的叶片惯性,但其中一些通过驱动系统使发电机减速。这通常导致驱动系统中的扭矩反转,这可能导致系统的惯性在减速时以系统的扭转固有频率彼此缠绕和展开几次。注:1 MW和2 MW涡轮机具有相似的自然频率,尽管涡轮机的尺寸差异很大。这些反转如何在轴承中产生冲击载荷?
快速反转轴承载荷区和未对准滚子上的冲击载荷,损坏其他类型设备中的轴承,可能导致WEA损坏。快速反转轴承负荷区也会降低轴承寿命。在TTR期间,齿轮箱中的每个轴承都会看到几乎180°的快速负载区反转,这可能会在滚子和滚道之间产生严重的冲击负载。所有引用的研究都认识到冲击载荷可能是应力引起的地下WEA损伤的来源,大多数研究结果都将其列为建议的主要候选。
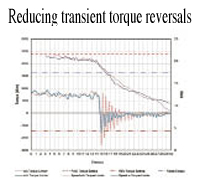
现场测试证明了降低最大反向扭矩和扭矩增加率的能力。该方法还可以抑制扭转
振动,将扭转次数减少到标称扭矩的40%。
在正常运行期间,轴承中的滚子在负载区时以预期或设计速度对齐并滚动。当它们离开负载区时,滚子减速,并可能在保持架的公差范围内错位。当它们再次接近负载区时,它们逐渐恢复对齐,并平稳加速以支撑负载。在快速加载区反转中,与正常加载区相对的未加载辊在这种未对齐状态下突然加载。这种快速加载增加了内圈中间滚轮的负载集中度。
虽然负载反转在许多类型的设备中是常见的,但风力涡轮机中常见的大小和速度的扭矩反转在其他设备中是罕见的。通常用于风力涡轮机齿轮箱的螺旋齿轮会增加额外的地下应力和应变。使用螺旋齿轮传动,每个圆柱轴承都会承受高轴向载荷,同时径向载荷会影响未对准的滚子。圆柱滚子可能轴向滑动并损坏滚道表面,通过点蚀和剥落进一步降低轴承寿命。滑动也会导致滚道磨损,导致微观裂纹,使水或腐蚀性油添加剂进入地下,从而引发氢致WEA。
如果径向冲击载荷太高,滚子会穿透油膜,则会产生足以防止轴向滑动的混合摩擦。轴向次表面应力将与径向冲击产生的赫兹应力相加,从而放大峰值应力。应变率也会被放大。超过WEA微观结构变化可能形成的阈值的可能性,解释了为什么WEA损伤在风力涡轮机齿轮箱中常见,而在大多数其他轴承应用中很少发生。圆锥滚子轴承也可能因负载反向的影响而损坏。由于热约束,用于高速和中速轴的轴承通常不会预加载,并且可能会出现损坏的轴向运动和冲击载荷。
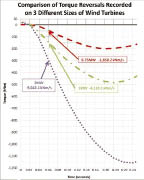
风力涡轮机的高分辨率扭矩反转记录反映了扭矩的变化率。坡度越陡,应变率越高。
在更大兆瓦级和多兆瓦级风力涡轮机投入使用之前,轴承的轴向裂纹问题并不是一种突出的故障模式。这不是早期小型涡轮机模型的常见故障模式,其中故障模式更常见的是点蚀和擦伤导致的轴承表面退化。轴向裂纹问题随着涡轮尺寸的增加而增加。
为了了解原因,重要的是放大现场数据,查看三台不同尺寸风力涡轮机上记录的第一季度或第二季度的最坏扭矩反转。在三种不同尺寸的风力涡轮机上记录的扭矩反转对比图比较了快速反转期间的相对扭矩大小和扭矩变化率。高分辨率扭矩监测设备记录的扭矩反转接近0.75、1和2 MW涡轮机高速轴上的涡轮机额定扭矩。在空气制动期间,涡轮机的扭转固有频率都相似,每个周期的振荡周期约为0.75秒。大型涡轮机的更高扭矩负载可以通过轴承的尺寸来调节,但油膜厚度不会增加。在扭矩反转过程中,任何滚子错位都容易导致更高的局部接触应力。扭矩反转过程中反向扭矩增加率的差异可能是一个更大的因素,因为它直接与滚子冲击时滚道中的应变率有关。较高的应力和较快的应变率都会增加瞬时塑性变形能量。
塑性变形能量存在一个阈值,其中产生的瞬时热导致基底材料的微观结构变化。大型涡轮机的应变率是否会超过该阈值?在快速载荷区反转过程中,滚子上快速增加的载荷是否会产生足够快的塑性变形,从而将轴承钢的微小条转变为超硬铁素体WEA夹杂物?当然,WEA微观结构改变的所有元素都同时存在。扭矩反转会吸收齿轮齿隙,并快速影响轴承空载侧的惰轮。错位的滚子会使滚子下的应力集中和塑性变形恶化,并引发混合摩擦接触。螺旋齿轮传动引起的轴向载荷的同时反转会在内滚道表面产生表面牵引力和附加应力。由此产生的高应变率和塑性变形可以解释WEA微结构转变的产生。
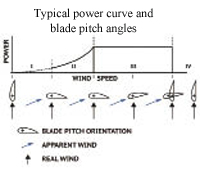
在典型的功率曲线中,可变桨叶片使现代风力涡轮机的性能接近理想的功率曲线。叶片定向和控制可使涡轮机最大化发电。
由于WEA棉条完美地放置在滚道表面之下,一个微小的棉条就足以引发WEA损坏,从而导致轴承轴向开裂、失效。只需要一瞬间就可以超过高负载和应变率阈值的组合。该事件可能来自一次严重的紧急停机,紧急停机与阵风、强风停机、控制故障或传感器故障的组合。一些研究人员表示,扭矩反转会产生高达标称扭矩2½至4倍的负载。这将是三种不同尺寸风力涡轮机上记录的扭矩反转比较中所示扭矩负载的2½至4倍。此外,如果固有频率不变,应变速率也会高出2½至4倍。在相同的自然频率下,扭矩大小每增加一倍,就可以有效地将导致WEA损伤的瞬时变形能量增加四倍。
滚子在轴承滚道上的快速和严重冲击载荷会导致应力引起的WEA损坏,从而显著缩短轴承和齿轮箱的寿命,有三种方法可以解决这个问题。
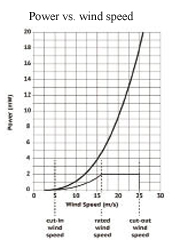
为了在大风期间提供保护,当风力接近25 mps的典型切断速度时,涡轮机将使用不到可用功率的10%。涡轮机的叶片将倾斜到一个精确的角度,以有效地释放风力,避免过度负载。
正在进行的研究应证明这些解决方案在延长轴承寿命方面的相对价值。一些建议的解决方案可以通过早期轴向裂纹检测逐步延长寿命或防止灾难性故障。非对称扭矩限制器解决了根本原因——快速而严重的载荷会引发应力引起的WEA损伤。简单的摩擦滑移扭矩限制器通常用于保护风力涡轮机驱动系统免受严重的扭矩过载,如发电机短路。然而,没有证据表明这种基本的扭矩限制器可以提供防止轴向裂纹的保护。不对称扭矩限制器的反向滑移设置要低得多。对带有或不带有不对称扭矩限制器的风力涡轮机进行的现场测试表明,其能够显著降低最大反向扭矩和扭矩增加率,从而在扭矩反转过程中滚子冲击轴承滚道造成的最大应力和应变率。这种方法还可以抑制扭转
振动,以减少反转次数。

红色虚线轨迹描绘了无不对称扭矩控制的750 kW涡轮机的扭矩反转幅度和变化率。蓝色轨迹与不对称扭矩控制相同,并显示其在降低最大反向扭矩和反向扭矩增加率方面的有效性。
750 kW涡轮机的现场数据显示了不对称扭矩控制在降低最大反向扭矩和最大反向扭矩增加率方面的有效性。冲击滚道的滚子的应力大小和最大应变率降低了50%以上。这意味着瞬时冲击和变形能量减少了75%。
在大型涡轮机上,这种变形能量的减少与显著减少轴向裂纹的可能结果类似。如果非对称扭矩控制将冲击载荷保持在WEA微观结构改变开始时的阈值以下,则超硬WEA条不会在滚道下形成,齿轮箱轴承中的轴向裂纹将不再是影响风力涡轮机能量成本的突出故障模式。
可倾斜叶片使现代风力涡轮机模型的性能接近理想的功率曲线。叶片变桨控制对于最大限度地从风中获取能量非常重要。此外,作为主要的安全制动系统,在涡轮机子系统发生故障时,保护涡轮机免受高风速、损坏风荷载和超速的影响至关重要。
典型功率曲线和叶片桨距角图表还显示了典型现代涡轮机的桨距角。在低风速下,叶片处于与转子扫掠平面成90°的完全顺桨位置。在区域II中,叶片旋转至约0°桨距角以获取最大功率,捕获接近50%的风力可用功率。在区域III中,叶片向后倾斜,以保护涡轮机在努力控制和保持全额定功率时免受高应力的影响。在切出速度时,叶片快速变桨,以提供制动,从而安全减速并关闭涡轮驱动系统。
功率曲线的功率与风速曲线掩盖了在强风和湍流期间保护涡轮机免受损坏的挑战。应变率分析图显示了与风力可用功率相比的涡轮机功率曲线。当风力接近25英里/小时(55英里/小时)的典型切断速度时,涡轮机可能使用不到风力可用功率的10%。叶片必须倾斜到一个精确的角度,以有效地释放风力,风力相当于涡轮机额定功率的10倍,并保护驱动器免受过度负载的影响。对于更长的叶片,在更低的风速下可获得切入速度和额定功率速度,从而显著提高了年度能源输出和财务绩效预测,同时也增加了控制过度风力负载的挑战。
在大风时,叶片已经向后倾斜20至30°,以释放大部分风力。在电网失电或紧急停机期间,叶片迅速进一步变桨,以使涡轮机减速。此时,扭矩反转和轴承冲击载荷的可能性处于最差的可能性。最高风速往往发生在风暴天气,此时阵风和湍流较大,电网损失和紧急停机的可能性最大。狂风期间的强风停机和紧急停机为驱动系统扭矩反转和轴承损坏的冲击载荷创造了完美的风暴。AeroTorque记录的最严重的扭矩反转发生在暴风条件下的大风停机期间。